What is Key Performance Indicator?
A Key Performance Indicator (KPI) is a measurable value used to evaluate the success of an organization, team, or individual in achieving specific objectives. KPIs are quantifiable, making them objective tools for performance assessment. They are closely aligned with strategic goals and are essential for guiding decision-making, motivating teams, and tracking progress over time. KPIs can be financial or non-financial and should be customized to fit the specific goals and needs of the entity using them. They are not only vital in measuring success but also serve as a communication tool, simplifying complex data into understandable and actionable insights. Essentially, KPIs convert abstract objectives into concrete targets, facilitating a clear understanding and improvement of performance.
Excessive friction: Increased friction between moving parts can generate heat, leading to higher surface temperatures. This can be caused by misalignment, lack of lubrication, or excessive wear.
Bearing problems: Faulty or worn bearings can generate excessive heat due to increased friction and poor lubrication.
Electrical problems: Electrical malfunctions, such as short circuits or loose connections, can cause overheating of components.
Mechanical imbalances: Mechanical imbalances, such as misaligned shafts or unbalanced rotors, can generate excessive vibration and heat.
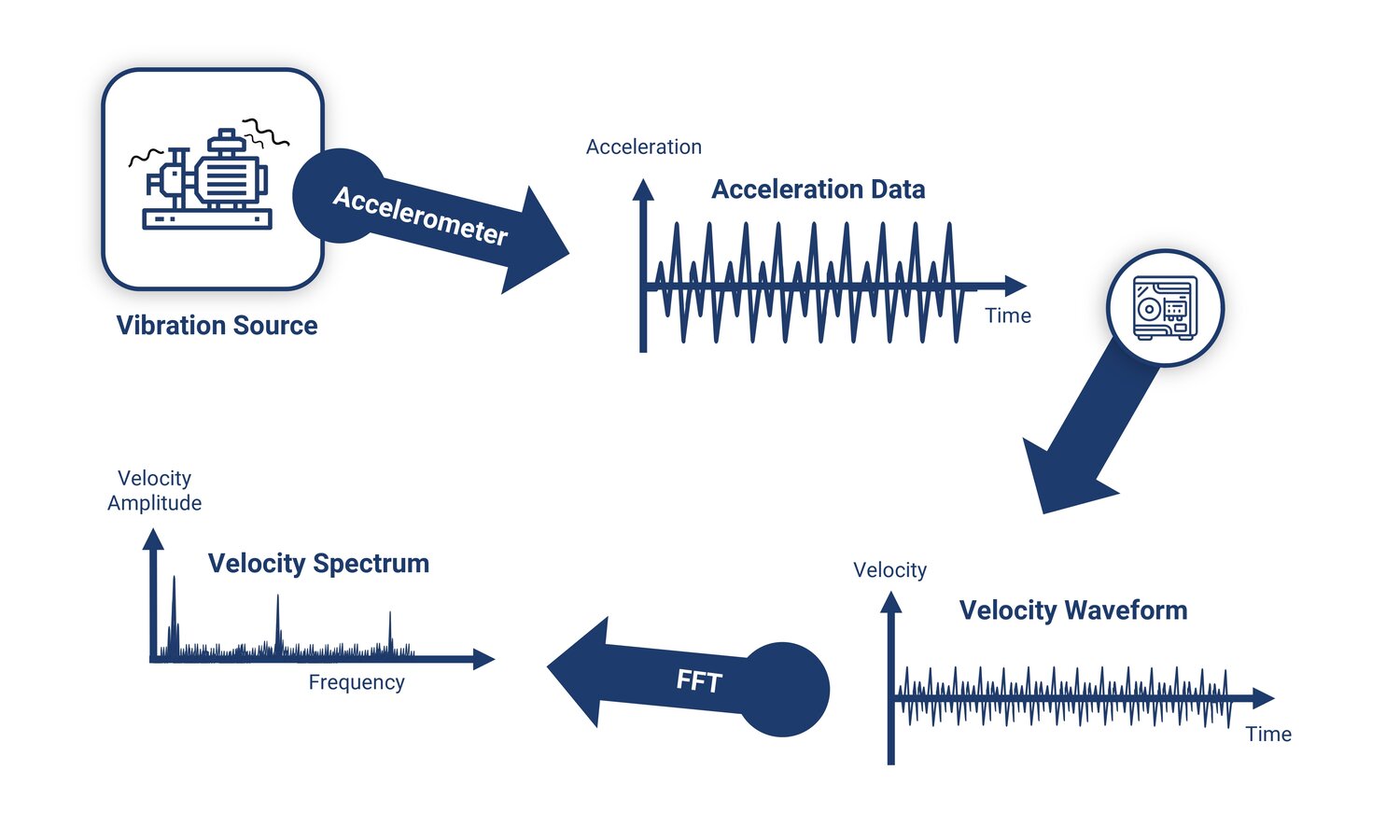
RMS vibration velocity and acceleration are measurements that provide an overall assessment of vibration levels. Elevated RMS values can indicate:
Bearing Defects: Worn or damaged bearings can produce increased vibration due to excessive clearance or misalignment.
Gear Mesh Issues: Faulty gear meshing can cause excessive vibration, leading to higher RMS values.
Shaft Imbalance: An unbalanced shaft can result in excessive vibration and elevated RMS values.
Loosened Components: Loose components, such as bolts or couplings, can vibrate excessively, increasing RMS levels.
Peak to peak vibration velocity and acceleration represent the maximum and minimum vibration values within a specified time frame. Abnormally high peak values can indicate:
Impact Events: Sudden impacts or collisions can cause high peak vibration levels.
Damaged Components: Broken or damaged components can generate excessive vibration, resulting in high peak values.
Misalignment: Improper alignment can lead to high peak vibration levels due to excessive stress on components.
Resonance: Operating at or near the machine's natural frequency can amplify vibration levels, leading to high peak values.
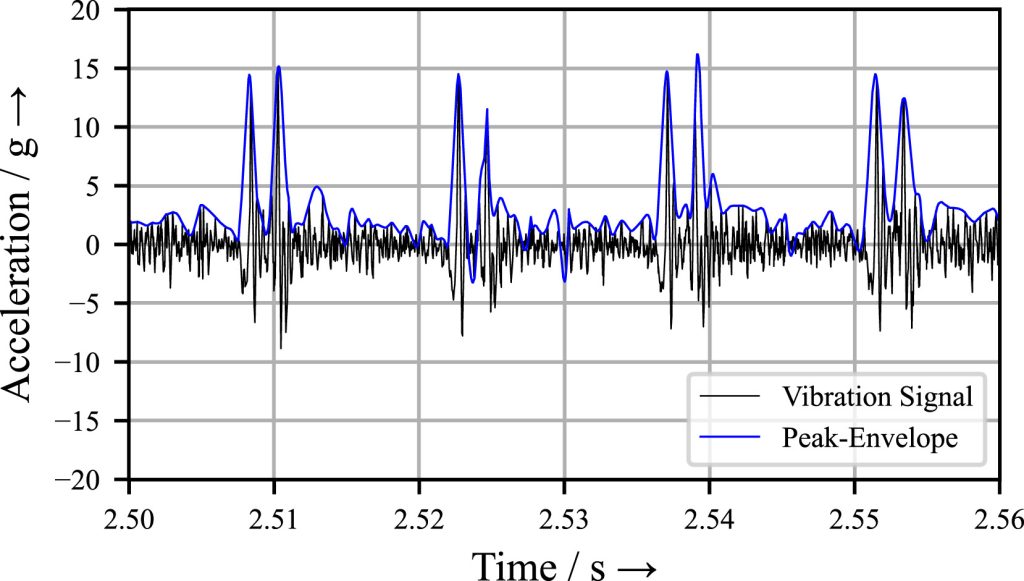
Zero to peak vibration velocity and acceleration represent the difference between the minimum and maximum vibration values within a specified time frame. High zero to peak values can indicate:
Bearing Defects: Worn or damaged bearings can produce increased vibration, resulting in higher zero to peak values.
Eccentricity: Eccentric components, such as shafts or rotors, can cause high zero to peak vibration levels.
Loosened Components: Loose components can vibrate excessively, leading to higher zero to peak values.
Rotor Imbalance: An unbalanced rotor can generate excessive vibration, resulting in high zero to peak values.
Crest factor is a measure of the sharpness or impulsiveness of a vibration signal. A high crest factor indicates that the vibration signal contains sharp peaks, which can be an indication of:
Bearing Defects: Worn or damaged bearings can generate high-frequency impulses, resulting in a high crest factor.
Gear Mesh Issues: Faulty gear meshing can cause high-frequency vibration, leading to a high crest factor.
Misalignment: Improper alignment can cause high-frequency vibration and a high crest factor.
Mechanical Loosening: Loose components can vibrate excessively, generating high-frequency impulses and a high crest factor.
Kurtosis is a measure of the peakedness or flatness of a vibration signal's distribution. Shortly, kurtosis expresses how similar the values of a signal are. Therefore, in case of a signal with many distinct peaks or impacts, the kurtosis will be higher. Abnormal kurtosis values can indicate:
Bearing Defects: Worn or damaged bearings can produce high-frequency impulses, resulting in a high kurtosis value.
Gear Mesh Issues: Faulty gear meshing can cause high-frequency vibration, leading to a high kurtosis value.
Misalignment: Improper alignment can cause high-frequency vibration and a high kurtosis value.
Mechanical Loosening: Loose components can vibrate excessively, generating high-frequency impulses and a high kurtosis value.